I made this a few years, ago but used it today and have never taken photos of it so thought you guys might like to see it.
occasionally when making models, one has to bend copper tubing. the typical tube bender, while successful in creating a bend, is not up to the task for modeling as 1) it won't work to a small enough radius and/or 2) distorts the shape of tubing around the curve - ie not a smooth transition from curve to straight on both the inside and outside curves. Thus began a bunch of experiments and reading on to produce a decent bend in a tube.
What I came up with has two unique (well they were to me anyway) features. 1) the outside die, rather than being a round die like the inner is straight. 2) the outside, straight, die, gets tightly pressed against the inner die, sandwiching the copper tube between them. This done via an eccentric axle. If you look in the pic, you’ll see the straight die, then a cylindrical spacer. It's this cylindrical spacer that is on an eccentric shaft.
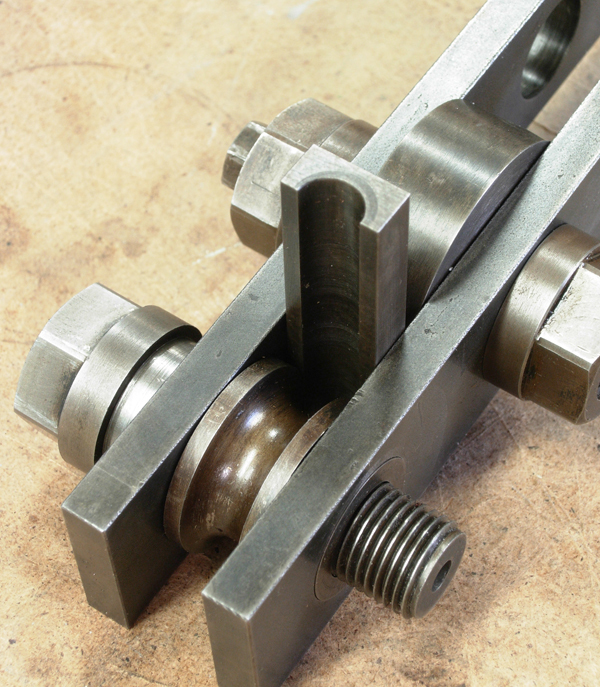
Here a bend is being set up. The tube clamp shows a larger allen key setting the orientation of the clamp along a tee slot, while the smaller one clamps the tube itself. I made slit spacers for different sized tubing. In the main pivt, about the round die, there are spacers such that it is firmly bolted to the base, yet free rotate.
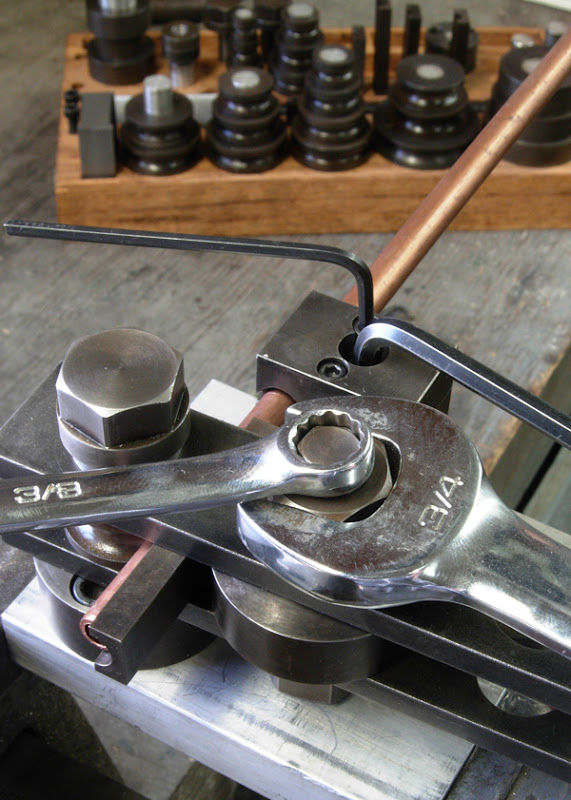
here's a shot after completing the first and second bends. the tube was annealed for these bends
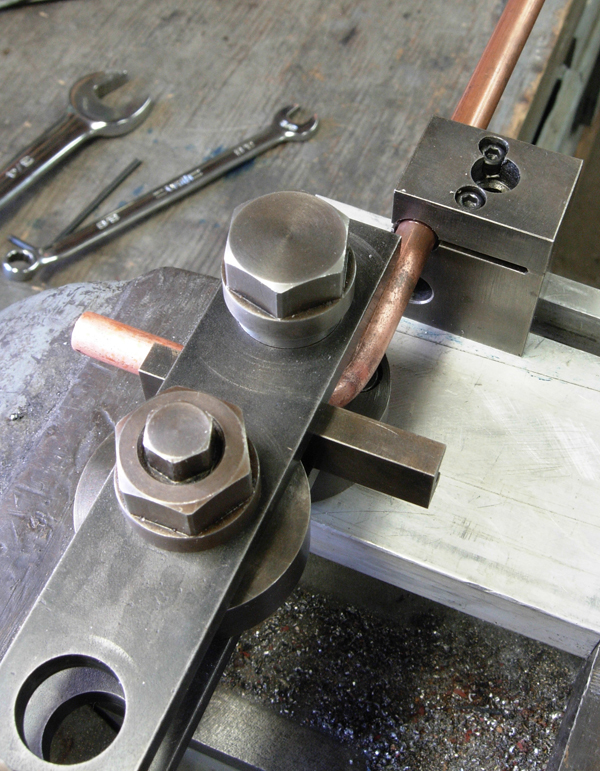
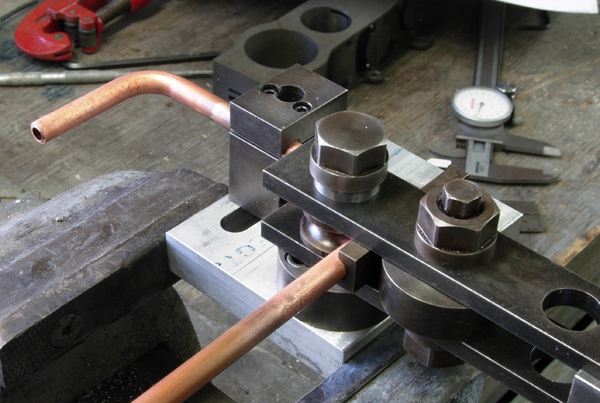
here's a close up showing the fairly decent shape that is maintained. ideally the bend looks like 1/4 of a torus without kinks or ploughed-up leading edge to the bend.
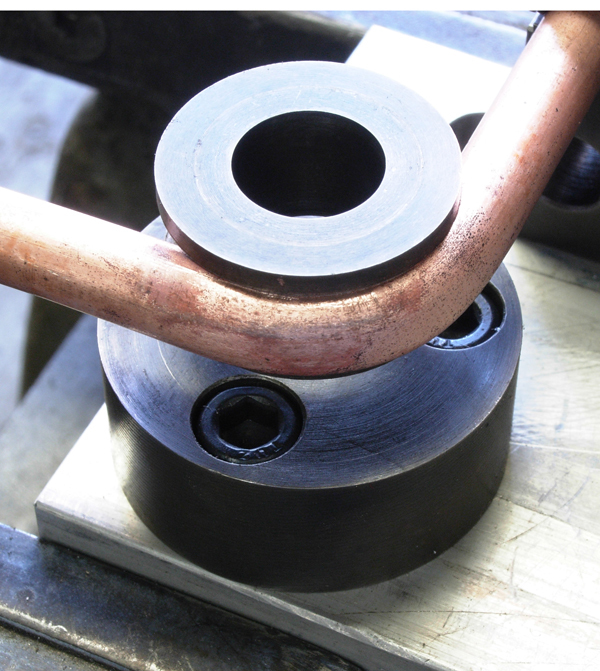
of course, if you're going to make a tube bender, you're going to do so for all sizes of tubes and radii. Should I ever commit a heinous crime, I consider this important work towards my insanity defense. It handles tubing from 1/8 to 3/8 by 16th’s
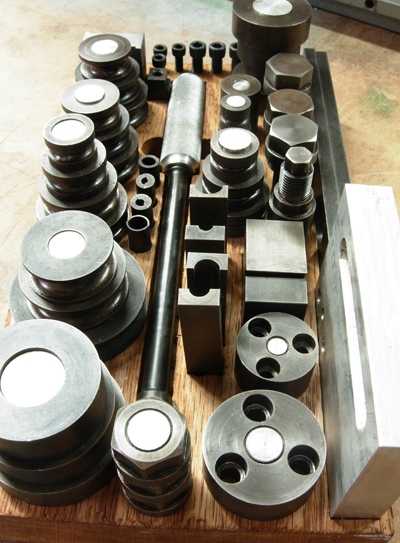
after cutting to length and some emery and polish work, here's the finished product. It’s sitting on the block to which it will one day be attached. Imo it turned our well, its a .5" centre radius bend in a 5/16 tubing. Still, the Stuart plans (this is for a triple expansion) calls for a 5/16 centre line bend, the accomplishment of which still eludes me, even with this rig. perhaps filling with cerro or something.
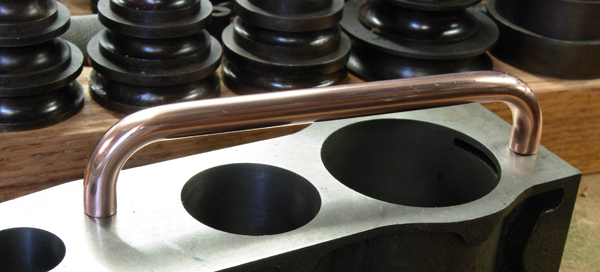
nothing is hardened, figured its low duty cycle and bending copper. I will probably use casenit on some parts, ie the top 3/8 hex on the pivot is starting to get dinged up. The finish is just the wipe on blue done to help fight rust.
here's the device i used to cut the radii. hardened a bit of drill rod with a clearance taper to it and then after hardening, surface ground it down to be the right dia. it work reasonably well, had I known about the 'up and over' style using a boring head and tangential cutter, might have gone that route

the tube comes in coils which isn't much good for my purposes. you can straighten it by tieing one end off to a tree and the other to a bumper, but that reduces the dia and is a pita in my urban environment (I'm sure the neighbors already think I'm certifiable, let alone if they keep seeing me out tying crap to a tree and to my car).
so i made this mill. the two upper rollers are adjustable. orginally they locked into position via a threaded collar and spanner (shown in the pic) however this wasn't positive enough so i added the hex screws to keep them in place. the middle roller, while it has a sprocket, pretty much idles. it works well and is powered used the table crank from my mill.
here's a few shots of it


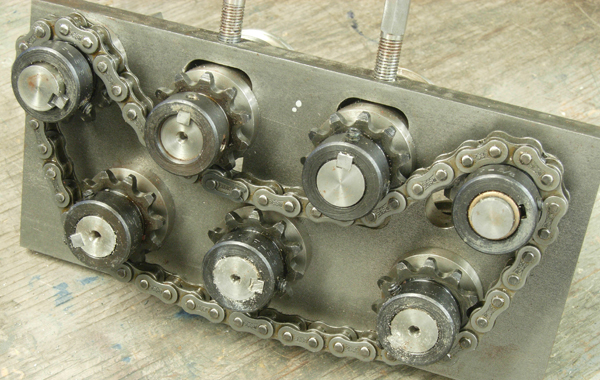