Here's some I've made and have used on various engines. in each case i held the casting in the lathe, covered the bed with paper towels. the laps float and hand held - you get a very sensitive feel on what parts of bore are tight. work your way up in grits expanding the lap every so slightly as you go. copper is the right material to use, the grit gets embedded in it. to save $$$ i solder thin copper onto a steel barrel.
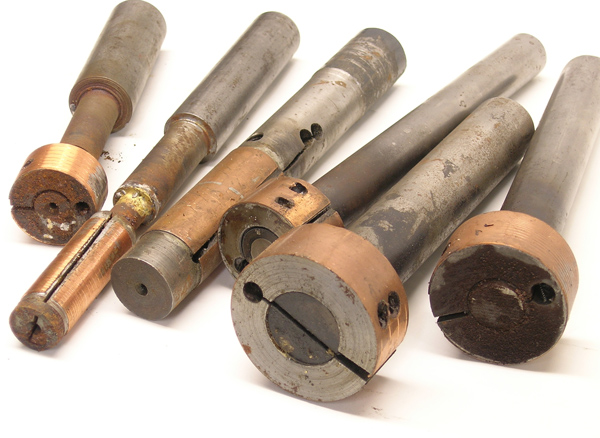
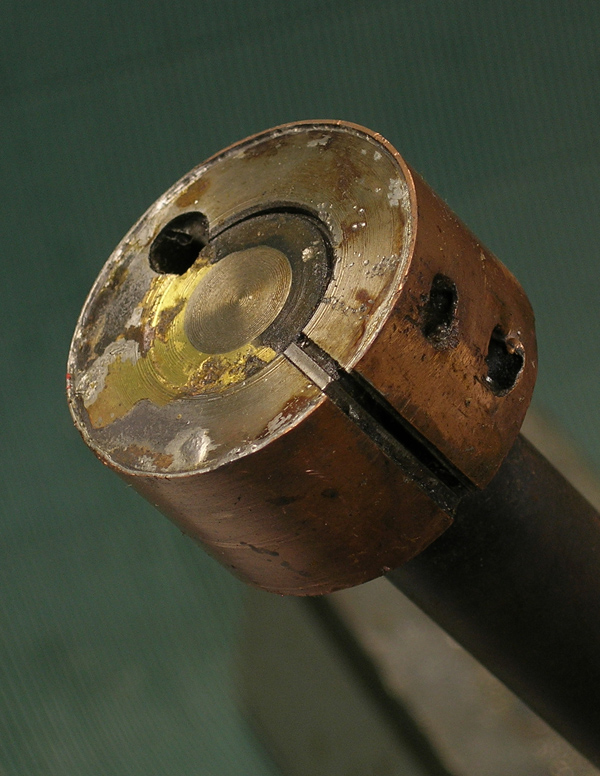
There was also a link posted to an short article he wrote about these:
http://metalworking.com/dropbox/_2002_retired_files/copper_laps.pdf
Note: This article seems to have been deleted from the dropbox.
On the HMEM board, Swede posted his technique for using laps:
Obviously your experience with honing has served you well. I tried a number of brake hones, and for me at least, it was a disaster. I know that there are some quality honing tools out there, such as Sunnen, which might help a new guy. As for lapping, the technique is to find a lap that is preferably longer than the bore, but that is not critical. The cylinder is bored in the lathe as best you can, leaving behind perhaps 0.001" to 0.002" for the final lapping. If your bore has no taper and a fine finish, you can get away with perhaps 0.0008", a little less than a thousadth. If the bore tapers, then you have to plan for the lap to eventually open up the bore to the widest part of the cylinder, plus another 0.0005" or so.
You then purchase or make a brass or copper lap like the ones in the picture, and if necessary turn it down with the expansion plug set at zero so you can get a fit of -0.001" or -0.0005", give or take. You need room for the compound.
The lap is charged. To charge a lap, mount it in a drill press, and select your paste. I start with Clover 320 grit, call it "medium" grit. If you have a lot of metal to remove, go to a coarser grit. Dab a bit of the paste onto the lap, and turn the drill on slow. Take a small steel flat, preferably hardened, and use it to distribute the paste all over the lap. Once you have an even coat, you use the steel flat to press, HARD, and this forces the grit INTO the lap metal. Then, remove most of the compound from the lap. When done, the lap has a frosty appearance and a rough feel, with dabs of compound resident in the grooves or holes of the lap's surface.
With Kerosene as a lube, or WD-40, the cylinder is installed onto the lap, and the lap expansion screw is tightened. The drill press is OFF, of course. Tighten the lap until you get a slight to modest resistance when you turn the cylinder relative to the lap. You should be able to turn the cylinder by hand.
Release the cylinder. Turn the drill press on its slowest speed. I will now describe a process which can be injurious if care is not taken. Be sure there are no sharp edges. This is the only case where I recommend a leather glove be worn when using a drill press, but ONLY if there is NOTHING that can possibly snag the glove. A "big boy" approach is definitely taken. To begin, you simply grasp the cylinder so that it stops revolving. There will be drag. Pump the cylinder up and down the lap, keeping a bit of the lap exposed on both ends. Within seconds, maybe 30 to 45, the resistance will fade; it will be easier to keep the cylinder stationary relative to the lap. Stop the lap when this reduction of resistance ends. The lap has cut as much as it will with that expansion set.
Take a look in the cylinder. You will see a frosted gray area, and area(s) that are "as bored" in the lathe. The frosted areas are the newly-lapped portions of the bore. Track the process with a good internal mike.
You then expand the lap a little, dab more compound onto it (thin it with kerosene or wd40) and reinstall the cylinder, this time flip the cylinder end for end. Repeat the process. Keep it liberally wetted with kerosene. It will make a bit of a mess. Each time you examine the cylinder, more and more it will be lapped vs. the original lathe turned bore. If the bore is slightly tapered, you can focus on the tight spots by dropping the cylinder's wide portions BELOW the lap, but keep it moving. The entire process by its very nature tends to create a true cylindrical bore. You have to WORK at it if you want to make a tapered bore.
At the end of the process, you can install a finisher lap with a finer grit, but really this often is not necessary, as you want the slightly coarser finish for an IC engine cylinder, as opposed to a hydraulic piston bore, which sometimes is a mirror!
I hope this helps someone... it seems a bit like voodoo, but it is surprisingly easy to do. For an IC engine, I recommend that you finish your cylinder, including lapping, before turning the piston(s) and making the rings, as you will base those measurements off of the bore's. And realize too it is no big deal if you go oversized a bit. An engine that is supposed to have a bore of 0.875" will run just fine if you end up at 0.879", so long as the rings and piston are turned to adjust for this larger bore.
Here's a small photo of the type of laps he uses:
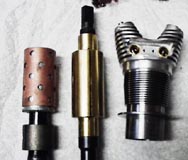
Bogstandard posted on the HMEM forum:
You can in fact use almost any material for the lap as long as it is softer than the part you are lapping. For steel, I use brass, for brass I use ali, for ali I would use a nylon rod.
You should make the lap a nice sliding fit into the bore, and ensure it is parallel along its length.
If starting off with a grinding paste, dab a bit of paste onto the lap, and roll it on a hard surface and use a piece of hardwood to embed the cutting agent into the lap. What you are doing is making a very accurate round file. For soft cylinder materials like brass or ali, on no account use one of the diamond lapping compounds, it embeds itself into the cylinder wall and will act like a file on your piston.
If possible make the lap a bit longer than the cylinder and always try to have the whole length of the cylinder on the lap at all times, this will tend to lessen the bell mouth effect.
Grinding paste will break down during use and go into smaller particles. You go from fine to finer compounds until you have a perfectly smooth bore. Normally you would then lap the piston to the bore, but in your case where you are using graphite, this can not be done, so the bore has to be smooth in its own right, then make the piston to fit.
The way I do it works for me, someone else might have different methods.
For your leaded steel I would start with fine automotive grinding paste (used for grinding in valves), at small pot will last you the rest of your life.
The lapping action is, have the lap in the lathe chuck running at a very slow speed, and feed the cylinder on to it, get ready to let go quick, just in case it 'bites' and starts to turn with the lap. It doesn't take long to lap a part, usually only a few minutes. The hand action is (and no dirty thoughts here) while moving the cylinder up and down the lap, use a bit of wrist action to give a twist to the up and down action.
Then when the first charge has stopped cutting and gone to a sludge, have a look at the bore. It should look a dull finish all the way along with slight herringbone scratch marks from the lapping. If there are any machining marks still in there, they will have to be removed by further lapping with the grinding paste. Just recharge the lap and repeat. It will be the machining marks that will cause damage to your very soft piston. You just keep repeating until ALL machining marks are gone.
In your situation where you won't have a metal piston to lap fit, what I would do is turn up another lap to fit the just finished rough lapped bore. Then using something like metal polish or t-cut, pop a bit onto the lap and repeat the lapping process. You can go finer and finer with the polishes, it just depends what you want the finished bore to be like.
What you do is make the piston to fit the bore, for graphite you can polish it down with newspaper wrapped on a bit of flat wood to polish the outside of the piston and bring it down in minute steps, but make sure you keep everything square.
If done really well, the piston should slide really smoothly thru the bore, but when you put your finger on the end of the bore, the piston should stay where it is in the cylinder, held by the vacuum caused by the piston trying to drop. That is of course if you haven't already put a mounting hole thru the piston. In that case a bit of sticky tape over the hole will allow you to carry out the check.