There are a lot of simple tools that I'd like to have in the workshop. Here's a list so that someday I might actually get around to making them.
Lead and brass hammers (for seating work into the vise, etc)
Thursday, March 13, 2008
Wednesday, March 5, 2008
Small shops
I love small shops. Particularly the ones that are in a building by themselves. Most of these seem to be owned by British model engineers. Seems like most Americans find room in a basement. There's something comforting about having just the amount of space you need.
Bogstandard posted the following about his shop on the HMEM board:
Here is a little insight into how I do things. First off I built a prefabricated sectional concrete workshop, 16ft x 9ft internal measurement after first laying a 6" thick concrete base, then fully lined the inside and ceiling with 2" insulation board faced with plaster. This keeps me warm in the winter with just a small fan heater.
This first pic shows my outside stash, all obtained from either the recycling yard or friends donations, the copper tubes on top are about 4" diameter, plus my sash weights which supply most of my cast iron.
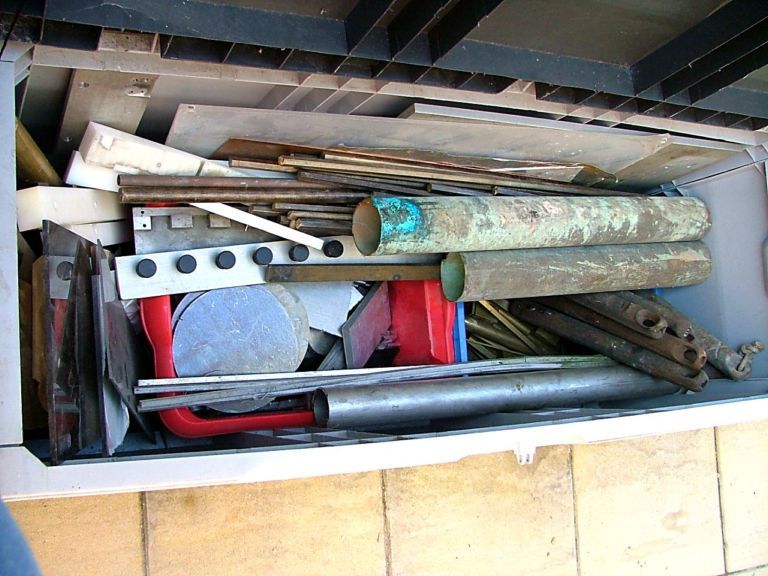
This next shot is coming in from the door, notice not a lot of room. the machinery consists of, on the left a 1960's Herbert surface grinder, in the middle an Atlas 10F 42" bed lathe and on the right a standard type mill drill with a cheap 3 axis DRO fitted. I have to go sideways thru the gap and usually end up with watering eyes because the handles reach parts other handles don't.
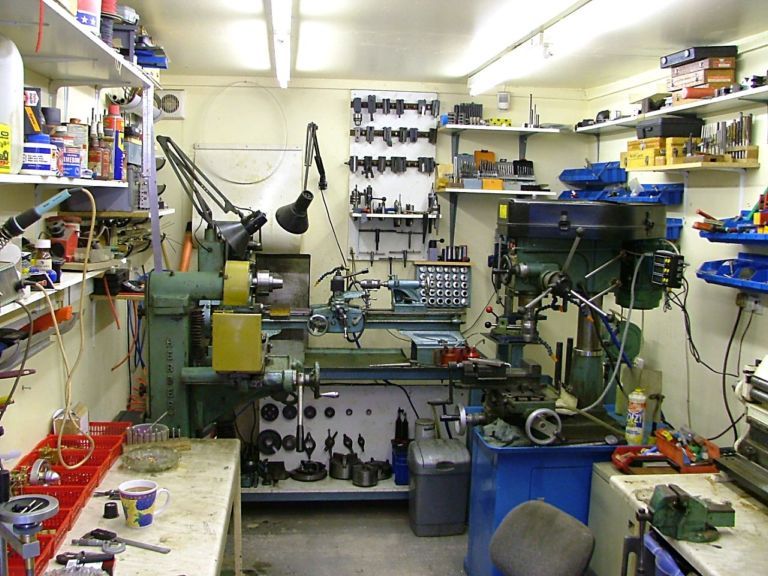
This one shows the shop from the machinery end with the metal prep area on the left and build area on the right.

Bit of a closer view of the metal prep area plus my inside stash on the bottom shelves.
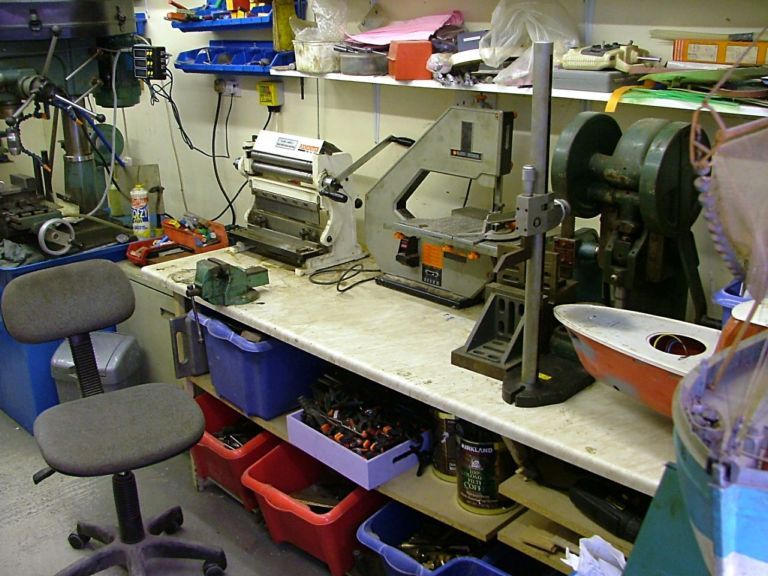
Build area consists of a small brazing/heat treatment area plus a marking out area. Next along is another marking area with my tapping stand followed by the engine build area.
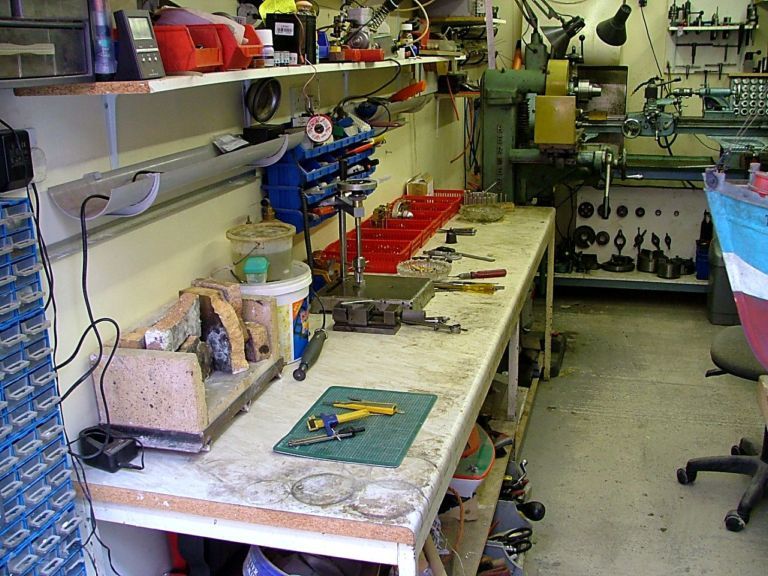
This last shot is my workhorse, The Atlas 10F lathe, nearly 70 years old, but I have brought it right up to date by fitting a Timken roller bearing head, Myford resettable dials, quick change toolpost plus loads of other small modifications. This lathe is now super accurate, especially since I fitted a 5c collet chuck.

About the green press with the flywheels, he says:
It is called a toggle press.
It is hand operated but the 'flywheels' help to make for a very strong punching press. With a correctly angled punch, 3/16" brass sheet is punched straight thru. I use it mainly for blanking out brass and copper discs and pressure assembly of parts.
Not many about nowadays, but if you can get hold of any old stuff, snap their hands off.
firebird posted about his on HMEM. Here's one photo:
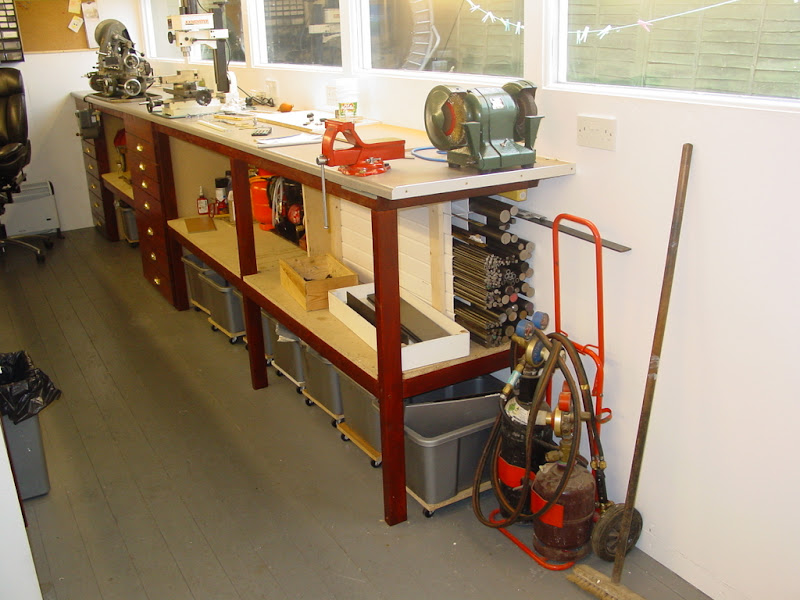
There's two things I particularly like about this. First is his long stock storage under the bench. The other is the containers he has on casters under the bench. Very effective use of space.
Bogstandard posted the following about his shop on the HMEM board:
Here is a little insight into how I do things. First off I built a prefabricated sectional concrete workshop, 16ft x 9ft internal measurement after first laying a 6" thick concrete base, then fully lined the inside and ceiling with 2" insulation board faced with plaster. This keeps me warm in the winter with just a small fan heater.
This first pic shows my outside stash, all obtained from either the recycling yard or friends donations, the copper tubes on top are about 4" diameter, plus my sash weights which supply most of my cast iron.
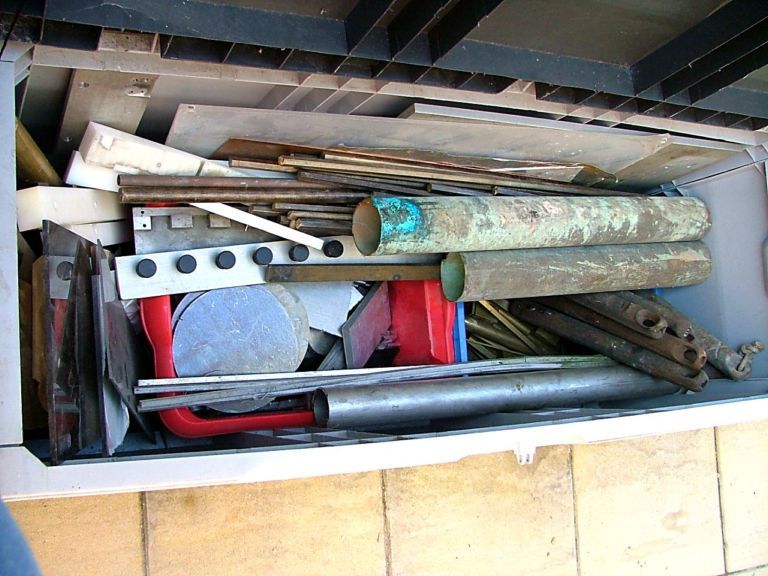
This next shot is coming in from the door, notice not a lot of room. the machinery consists of, on the left a 1960's Herbert surface grinder, in the middle an Atlas 10F 42" bed lathe and on the right a standard type mill drill with a cheap 3 axis DRO fitted. I have to go sideways thru the gap and usually end up with watering eyes because the handles reach parts other handles don't.
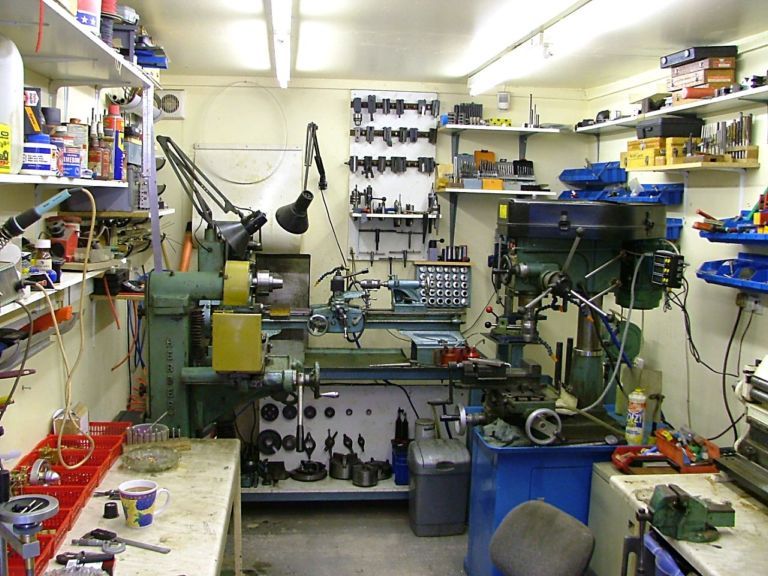
This one shows the shop from the machinery end with the metal prep area on the left and build area on the right.

Bit of a closer view of the metal prep area plus my inside stash on the bottom shelves.
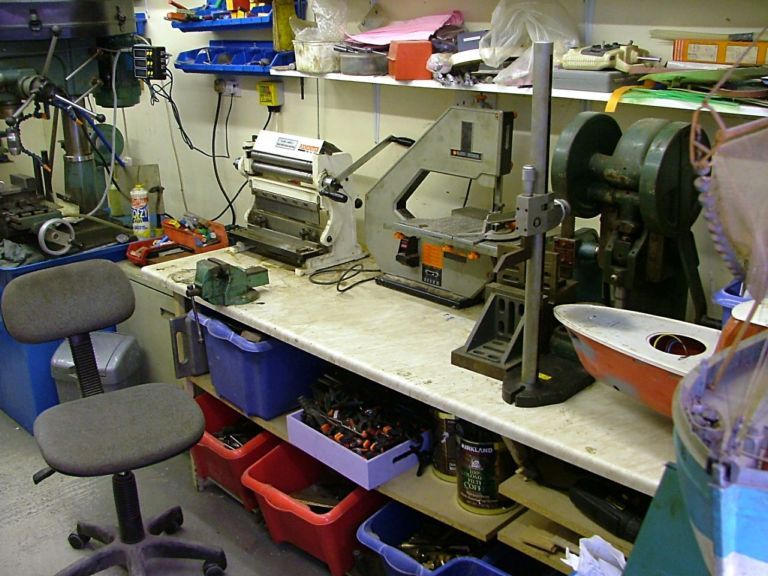
Build area consists of a small brazing/heat treatment area plus a marking out area. Next along is another marking area with my tapping stand followed by the engine build area.
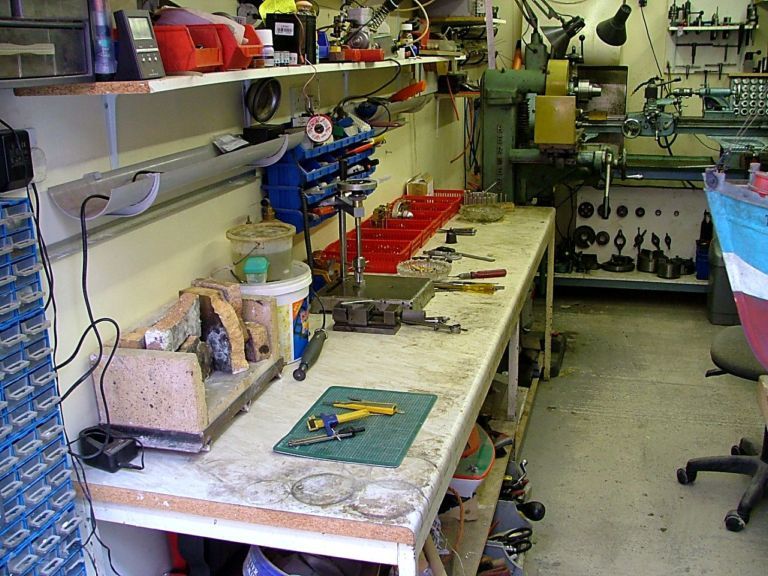
This last shot is my workhorse, The Atlas 10F lathe, nearly 70 years old, but I have brought it right up to date by fitting a Timken roller bearing head, Myford resettable dials, quick change toolpost plus loads of other small modifications. This lathe is now super accurate, especially since I fitted a 5c collet chuck.

About the green press with the flywheels, he says:
It is called a toggle press.
It is hand operated but the 'flywheels' help to make for a very strong punching press. With a correctly angled punch, 3/16" brass sheet is punched straight thru. I use it mainly for blanking out brass and copper discs and pressure assembly of parts.
Not many about nowadays, but if you can get hold of any old stuff, snap their hands off.
firebird posted about his on HMEM. Here's one photo:
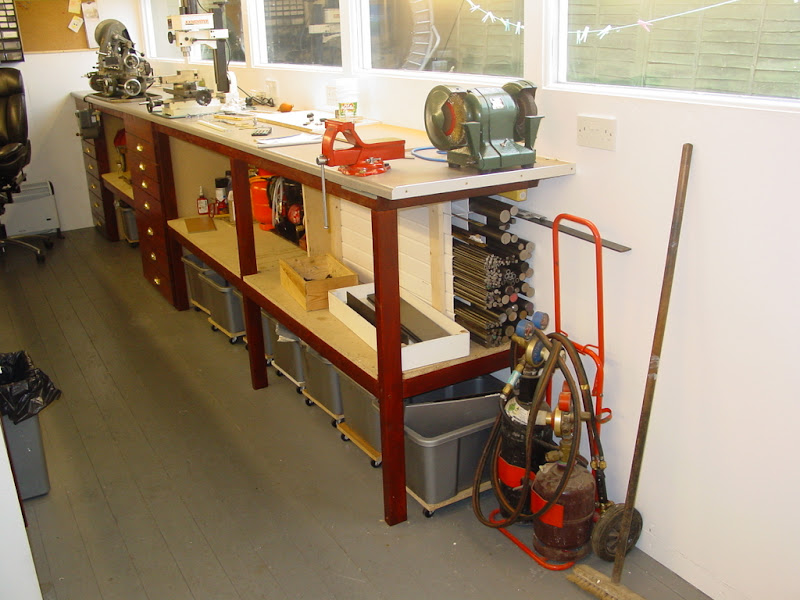
There's two things I particularly like about this. First is his long stock storage under the bench. The other is the containers he has on casters under the bench. Very effective use of space.
Subscribe to:
Posts (Atom)